To address this threat, railroads will need to make quantum leaps in both technology and operations. Simply keeping up with trucking technology changes won’t be enough: Railroads must look to be resilient, market-responsive, and future oriented. In our view, there are five critical areas where railroads could “disrupt from the inside” to help drive innovation and growth.
#1 AUTOMATING FASTER
The specter of driverless trucks is getting closer every day. Platooning, in which one driver controls several following trucks, is being tested in multiple locations and may soon be a commercial reality. But driverless trains are equally possible; in the US and Europe, railroads are halfway there, thanks to positive train control systems (PTC), which allow trains to be monitored and stopped remotely, and trip optimizer systems (a form “cruise control”), which optimize fuel consumption.
Mining giant Rio Tinto is currently testing autonomous trains in Western Australia, which suggests that arduous and remote routes might be ideal for initial deployment. Even if regulation or labor contracts aren’t there yet, railroads can start getting ready for more automation. For example, track and rolling stock inspection could be automated by equipping locomotives with smart track sensing technology, while detectors on railcars could monitor wheels, bearings, and brakes for problems. Through machine learning, train dispatching could leap the final hurdle into monitoring trains without human intervention.
AUTONOMOUS TRUCKS: GOING FARTHER AND FASTERTRANSIT TIME VERSUS DISTANCE
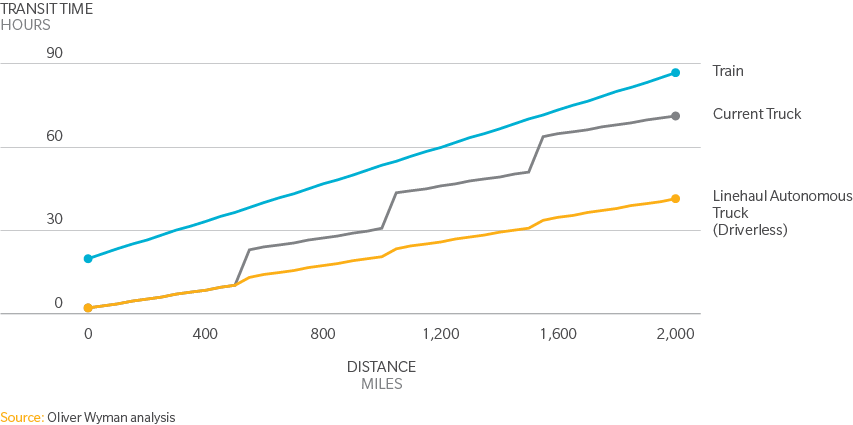
#2 IMPROVING FUEL EFFICIENCY
Currently, commercial diesel trucks get seven or eight miles per gallon. The US Department of Energy’s SuperTruck program has pushed that to 12-13 miles per gallon – making such trucks cost effective at longer distances. The next phase, SuperTruck II, is now underway, with the goal of doubling baseline fuel efficiency.
The trucking industry also has been willing to experiment with alternative fuel options. For example, United Parcel Service has 4,000 liquid natural gas (LNG) and compressed natural gas (CNG) trucks in the US, while some 550 LNG/CNG fueling stations have been built around the country. Tesla and Mercedes are building all-electric trucks, and Nikola Motor, Toyota, and Peterbilt are incorporating hydrogen fuel cells into hybrid trucks.
Some fuel-efficient rail technology has moved forward in Europe; less so in the United States. But future generations of locomotives will have to be more fuel efficient as trucking fuel costs drop. Feasible options might include hybrid locomotives that can capture regenerative braking energy, locomotive electrification, and hybrid fuel cells (see “What’s Next for Locomotive Technology?”). New technologies could be tried first in low-risk, local environments with a view to scaling up the most promising ones.
WHAT’S NEXT FOR LOCOMOTIVE TECHNOLOGY?
Most freight moving by rail is pulled by diesel-electric locomotives. But that technology is pushing up against the limits of what it can achieve while still improving fuel efficiency and reducing operational costs. In the US, for example, that “virtuous cycle” recently broke down entirely, when new government mandated emissions cuts actually increased the amount of fuel locomotives must burn. As truck technology improves, railroads will need to look elsewhere for innovations to stay competitive.
Liquid natural gas (LNG) has been tested by railroads since the 1980s. It offers lower fuel prices and emissions but has made little headway, given the cost of LNG fueling infrastructure, the difficulty of using dual fuel systems, and the decline in diesel fuel prices. One regional railway in the US, the Florida East Coast Railway, has completely converted to LNG, but it has only 360 miles of track, rather than the tens of thousands of miles of major US railroads. The railroads may need to look more carefully at how trucking is innovating with LNG, i.e., start in the terminal areas first and then scale up promising technology on main lines, rather than converting main lines on the first try.
Hybrid locomotives run on diesel fuel but have on-board batteries to help improve fuel efficiency. For example, DB Cargo AG is partnering with Toshiba to convert 300 older locomotives to hybrids. Most hybrid locomotives also employ regenerative braking, to capture and store the kinetic energy from slowing down in the batteries. This alone can reduce fuel consumption and emissions by up to ten percent.
A fast hybridization option could be to add battery tenders (specialized cars) behind existing locomotives, enabling fast swapping and off-train recharging. This could drastically lower fuel needs and maximize regenerative braking potential. These battery boxes on wheels could then be recharged at solar, wind, or natural gasstations.
Electrification, while not much used for freight in the US, is common in Europe. It can reduce energy and maintenance costs, and generates zero emissions from the locomotive (and zero overall if renewable energy is used to generate the electricity). The International Union of Railways estimates electricity costs are only 50-60 percent of diesel.
The biggest stumbling block to date has been the cost of catenary (overhead wire) infrastructure, but that might be changing: New super-capacitors could make up to 95 percent of trackside electrical systems unnecessary, by enabling on-board energy storage between recharging stations. Electrification of high-speed and high-capacity main lines could become much more realistic from a cost perspective.
Finally, hydrogen fuel cells provide continuous power, supplemented by a battery for peak power. Hydrogen fuel cells are attractive as they produce zero emissions other than water and are more energy efficient than combustion engines. Plus, liquid hydrogen can be created using renewable energy sources. There are still issues to work out, however, including increasing hydrogen storage capacity and travel range, and the need for hydrogen fueling infrastructure.
As this brief survey shows, railroads do have technology improvement options. Partnering with relevant innovators could be one route to determining if old technology ideas might now be more viable or if technology ideas from other industries could be adapted. But the changes needed in the future will be more than the merely mechanical: they also will require fostering an innovation culture and the willingness to break down barriers to change.
TRUCKING VERSUS RAILPACE OF TECHNOLOGY ADOPTION
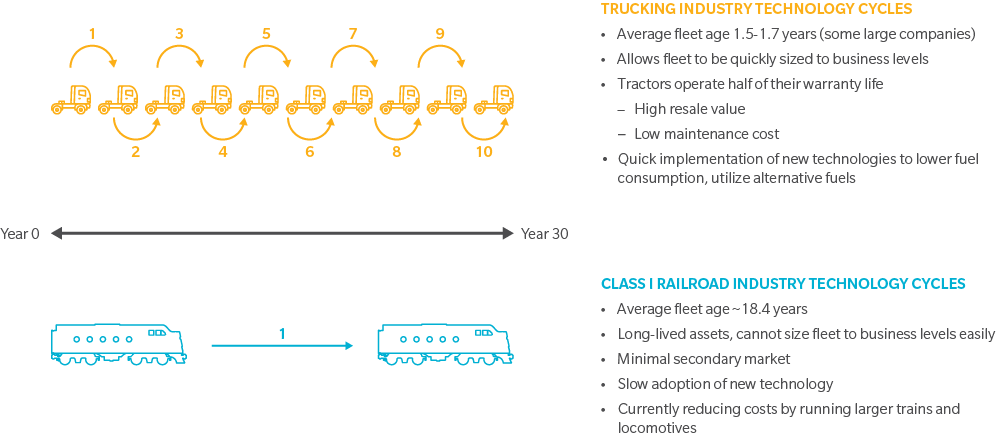
#3 REPLACING ASSETS FASTER
The life cycle of the average commercial truck is only 3-4 years. This means less maintenance overall and the ability to realize technology innovation benefits quickly. For example, the maintenance costs of new hybrid fuel cell/electric trucks unveiled last year are almost nil.
By comparison, locomotives are engineered to last 30 years and railcars 50, meaning they need increasing maintenance as they age. And while they last a long time, they don’t get any better. This is why we replace our cell phones every 2 years, our computers every 3 or 4, our cars every 5 or 6 – because today’s rapid technology cycles improve efficiency and add features. Perhaps locomotives and railcars only need to be designed for 10-15 year lifespans, to take advantage of the breakthroughs that could cut both operational and maintenance costs.
#4 MAKING BETTER USE OF ASSETS
Both business-to-consumer and business-to-business companies are being forced to restructure their supply chains: smaller shipments, more frequent service, higher reliability. What this means for the rail industry is that many trains are now too large. They spend a lot of time waiting around to be filled, and rail assets – from cars and locomotives to train crews and yard space – potentially could be used more efficiently. More frequent and smaller trains would be more responsive to today’s supply chain needs – while also maximizing the use of assets.
In the future, predictive analytics and machine learning (“smart railcars”) could offer yet more options to improve asset usage – but ongoing research and testing will be necessary to find out.
#5 CLAIMING MORE OF THE SUPPLY CHAIN
Large railroads are used to doing one thing well – moving large amounts of goods over long distances. Their presence in other links in the supply chain is often limited. Instead, intermodal marketing companies (IMCs) manage lucrative intermodal goods shipments, while other private operators manage first- and last- mile services (shortlines, auto ramps, intermodal and transloading terminals).
It might be time for railroads to get out of their operational comfort zone. There’s no reason a railroad couldn’t expand its ownership of ramps and terminals or broaden its use of joint rail-truck operations. Railroads already possess the necessary freight management skills and supporting information technology, so growing along the supply chain might be the ultimate competitive edge.
PUTTING IT ALL TOGETHER
Railroads have all of the building blocks to take advantage of changing technology and market imperatives. The critical issue is less one of playing catch up than determining how to assemble those pieces into a pattern that fits with the new digital economy. In short, by embracing reinvention and risk, the railroad industry can realize the vast potential that disruption has to offer.