Over the past decade, textile manufacturing fell by 28 percent, lumber and paper production by 27 percent, and computers and electronics by 23 percent. Increasingly, large segments of the public in the United States feel that the US is losing its industrial base and that steps should be taken to protect American manufacturing jobs.
Despite the perception of it being in dire straits, the reality is that US manufacturing is much more robust and in better shape than what the public discussion would suggest. Indeed, manufacturing is on the upswing in the US. That is not to say traditional factory jobs will be returning to these shores anytime soon: those traditional blue-collar jobs are never coming back – not however because they have disappeared to China or Mexico, but because of the effects of automation and digitalization, which have done away with the need for manual workers. But those very trends are giving rise to the need for a new kind of factory worker, one who is comfortable and has the skills to operate in a highly automated manufacturing environment. To take advantage of the manufacturing jobs that will be created in the coming years will require a significant upgrade in the skills and tech-savviness of the new manufacturing workforce.
A global secular trend
Declining manufacturing employment is a fact in every industrialized country, and is taking place at similar rates: As noted earlier, the past decade saw 0.6 percent annual decreases in manufacturing jobs in the US, with 1.4 percent in the European Union (EU) and 1.3 percent in Japan.
The primary force driving this secular trend is increased productivity due to advanced automation. Productivity in the manufacturing sector in the US has increased 3.0 percent annually over the past 10 years, with 2.6 percent annual increases in value-add, despite diminishing employment. Value-added features and activities are ones that change the form, fit, or function of the product and that the customer is willing to pay to have done. Indeed, US manufacturing productivity exceeded that of other developed nations. (See Exhibit below.)
Manufacturing productivity in the US has topped other nations
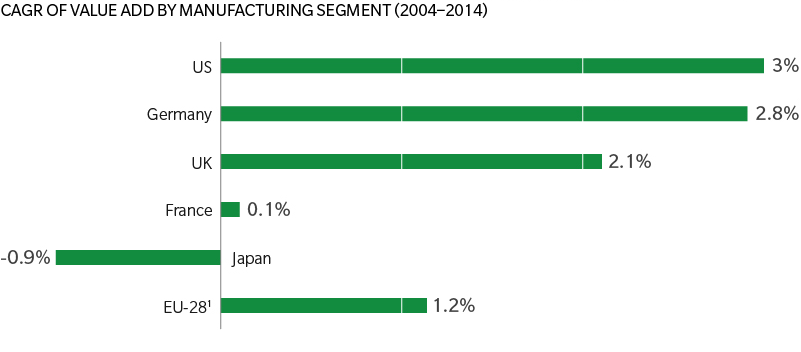
*1 Compound annual growth rate (CAGR) for 2004–2013
Source: OECD, Oliver Wyman analysis
US manufacturing is strong
America’s annual, 2.6 percent increase in manufacturing value-add points to the industry’s strength. Indeed, its value-add growth has outpaced that of the economy at large.
US manufacturing is also gaining a greater share on the world stage and benefiting from global trade: Exports have grown 5.2 percent annually (as compared to the EU where manufacturing exports rose 4.5 percent, Germany 3.1 percent, and Japan 0.3 percent).
5.2 percent growth of US manufacturing exports annually.
Moreover, the future bodes well for the sector. Deloitte’s Global Manufacturing Competitiveness Index (GMCI) places American manufacturing on an upward trajectory. Ranked fourth in the GMCI in 2010, US manufacturing took second place on the index’s 2016 ranking, behind only China. It is projected that the US will rank first in the GMCI in 2017 and is likely to maintain leadership over the next decade.
The importance of supply-chain management is strengthening American manufacturers: US manufacturing is increasingly embedded in global supply chains. For example, the share of foreign components in US car exports increased from 24 percent in 2000, to 35 percent in 2011.
Digital industry secures US manufacturing’s leading position
The next wave of efficiency gains in global manufacturing will be driven by digitalization and big data. Greater automation will render low-cost labor less meaningful in deciding where to build and maintain manufacturing facilities. Instead, speed, customization, and proximity to customers will be key. Consequently, value-added activities will, to a certain degree, gravitate back towards industrialized countries. The US will be a major winner. The European sportswear maker Adidas, for example, just announced plans to build a “Speed Factory” outside Atlanta, in order to be able to produce sneakers quickly and satisfy surprise surges in demand for product.
Blue and white collar jobs
However, the kind of manufacturing “returning” to the US will be very different from the manufacturing of old. Highly automated and flexible, it will require few new blue-collar jobs. Adidas’s Speed Factory, for example, will produce 500,000 pairs of shoes per year, while employing just slightly more than 100 employees. This tiny human workforce will be supplemented by the enterprise’s true producers: robots and 3D printing. A $1.2 billion plant modernization program recently announced by Ford will create a mere 130 additional jobs in the US.
The requisite skills will change too: Jobs on the shop floor will require more skilled workers, with science, technology, engineering, and math (STEM) knowledge, problem-solving skills and programming familiarity. Such talent will be scarce, and the traditional blue-collar job will not return.
The greatest efficiency gains will occur in the white-collar sector: Traditional white-collar jobs will be at the center of the next generation of manufacturing efficiency gains. Increased automation and digital industry will bring lean process improvements to manufacturers' back and middle offices. Many administrative functions will be automated, and the need for human employees diminished. Fields affected will be sales and maintenance planning, production scheduling, pricing, and inventory management, along with many others.
What can companies do and what role should government play?
Massive changes are coming to the workforce, changes that will affect companies and governments, equally. Firms can expect to see both a shortage in skilled workers and a glut in unskilled and unprepared candidates for jobs.
To meet the challenge, companies and governments must become more proactive in their approach to managing the workforce of the future. Firms should address the imminent shortage of necessary, skilled workers by instituting internal training/retraining programs to teach workers the skills they will need. Looking ahead, companies must seek to engage with STEM programs at local schools to ensure that graduating students are prepared to enter the workforce and to make a valuable contribution.
Manufacturers should be prepared to foster initiatives that reap the benefits of digital industry with respect to planning and administrative functions. This will mean retraining employees in analytics, big data, and modeling to prepare them for future job requirements.
Finally, it is critical that companies take the long view, particularly now when there is still time to prepare: Anticipate changes in skill requirements over the next three to five years and develop programs to address the shortcomings of your workforce.
Government can help reduce the shortage of skilled labor through increased support of organizations funding apprenticeship programs and initiatives for digital manufacturing education.
Preparing yourself for the factory of tomorrow, today
US manufacturing is actually healthier and in better shape than headline numbers and public perception would have it – which is not to say that old-time factory worker jobs are coming back to US shores. Indeed, it would be best to dispense with the fantasy of bringing back traditional assembly-line jobs: They are never coming back, not because Mexico or China, but because robots and automation are taking the place of people on the factory floor.
Human beings will still be necessary in manufacturing but to work in the factories of the future, they will need a significant increase in the STEM skills and aptitude they bring to the job. Today is the time for manufacturers, government, and workers to prepare for the automated and digitalized factory of tomorrow.
About Authors
Thomas Kautzsch is a Munich-based partner and global leader of Oliver Wyman’s Automotive and Manufacturing Industries practice. Andrew Chien is a Detroit-based partner and leads Oliver Wyman’s North-American Automotive and Manufacturing Industries team.