The demand for recycled plastic is growing much faster than the supply: Where the gap was 1.1 million tons just in Europe in 2023, we expect that shortfall to quadruple by 2040. Globally, that shortage of recycled plastic will inevitably force industrial users to continue their reliance on virgin plastic — further clogging landfills, polluting oceans, and hamstringing decarbonization and pollution reduction strategies for many industries.
Manufacturers of food and other consumer products are a good example of the impact of the shortage. Where most companies in these sectors plan to increase their use of recycled plastic in packaging to cut emissions and meet targets that minimize their impact on nature, a lot more recycled plastic would need to be available — 4.5 million tons by 2040 in Europe alone — for those decarbonization strategies to be fully realized.
The goal is possible. Current mechanical recycling significantly limits the potential uses of recycled plastic, usually confining it to its original purpose because of the quality of the recycled output. But with new processes that break down polymer chains and return plastic to its original compound, more plastic could be reused, and the chemicals industry could close the supply gap.
It’s an opportunity for chemicals to seize a leading role in plastic‘s circular economy, instead of leaving it to the currently dominant waste management industry. The capital investment required to get chemical recycling to commercial scale is steep, and initially selling recycled plastic would compete with the chemicals industry’s virgin plastics revenue. But given the waste problem plastics presents, many governments — particularly those in Europe and North America — have already begun to compel industrial plastics consumers to use recycled content in production and packaging. That required recycled percentage is expected to continue to rise, and it is only a matter of time before other nations follow suit.
Plastic pollution
Considered an industrial breakthrough a century ago, synthetic plastic today has become more of a problem than a solution. The eight billion tons of plastics produced worldwide over the decades now overwhelm landfills and pollute landscapes and bodies of water around the world. Discarded plastic has become one of the planet’s most pressing environmental problems.
Exhibit 1: The recycling rate of plastics compared to other materials (%)
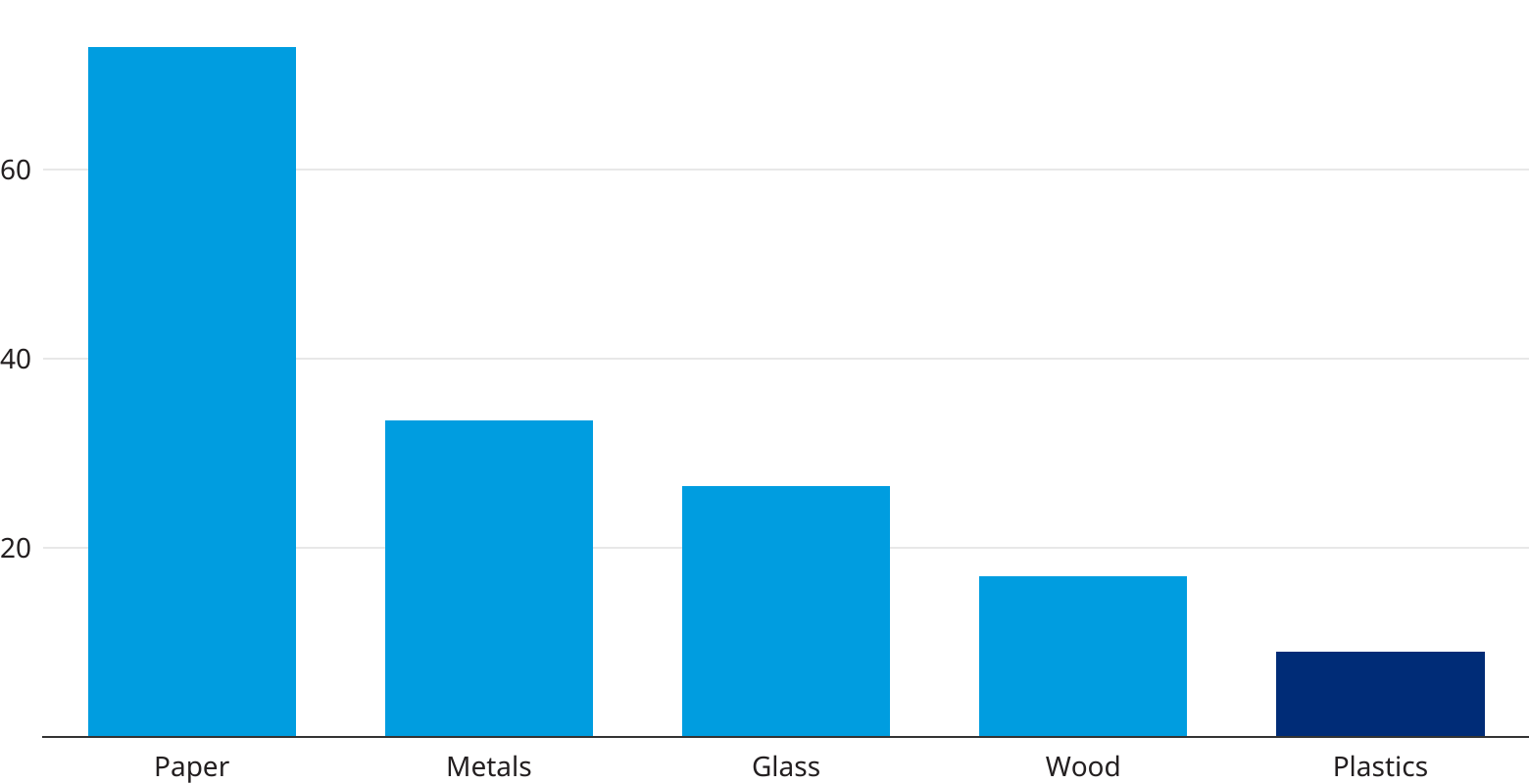
Source: Refinitiv Eikon, UNEP, EPA, European Commission, Oliver Wyman analysis
If the goal is to protect nature, then a top priority of the global economy must be rethinking its reliance on single-use plastics. That would require moving away from plastics altogether or switching to chemical recycling, a process that uses heat, chemical reaction, or both to break down used plastic to raw materials for the production of new plastic, fuel, or other chemicals. Chemical recycling allows plastics to be reused many times over and for different purposes.
Two of the most developed chemical recycling technologies are pyrolysis and gasification. Both make it possible to break down polymer chains of any kind through a high-temperature process, reverting the plastic to its original petrochemical compound. Both require moderate to high energy consumption, meaning renewable energy would need to be used to reduce potentially high emissions. Neither technology comes cheap.
There are other experimental technologies emerging or in development. At this point, based mostly on economics of the business, all face obstacles.
Economics differ
While mechanical recycling — the only commercial-scale form today— incurs operating process costs of $50 to $200 per ton of plastic, chemical recycling costs $300 to $1,000. So far, chemical recycling has been confined to demonstration plants and smaller factories. But processing costs should fall with the expansion of processing facilities and the creation of economies of scale.
Currently, only 9% of plastics produced gets recycled. That significantly trails other materials like paper, which recycles almost three-quarters of production and metals, which recycles more than 30%. Besides moving away from single-use plastics, part of the challenge will be increasing recycling behavior worldwide. Right now, Europe and North America have recycling regulation covering more than 80% of their populations. In contrast, the Middle East and Africa have recycling regulation covering only about one-third.
Developing chemical recycling capacity is a way for chemicals to catch up to the more dominant waste players already in mechanical recycling where large buyers of recycled plastics like beverage companies are increasingly entering into partnerships with waste management operations. These collaborations provide consumer goods manufacturers a guaranteed supply of recycled plastics and recyclers with certainty of demand. This becomes especially advantageous when shortages in either feedstock or recycled plastics exist.
Moving to chemical recycling
But eventually these disposal players or large-scale consumers of recycled plastics may also look to adopt chemical recycling because of the feedstock flexibility it provides. The partnerships between customers and disposal companies, already working today in mechanical recycling, could lead to the establishment of chemical recycling plants by the same players, which would put the chemicals industry in danger of losing direct access to raw material.
Players are already jockeying for the best starting position in this race to develop the recycling industry, so the chemicals industry cannot afford to drag its feet. To respond, chemicals companies have numerous options. They can enter into joint ventures with disposal companies, as LyondellBasell and Suez did in 2018. The joint venture Quality Circular Polymers, which LyondellBasell now controls, has grown significantly since then with the acquisition of TIVACO in 2020 and collaborations with major consumer goods companies like Samsonite. Another matchmaking example: TotalEnergies and Paprec, the leading recycling company in France, have entered into a technology partnership for chemical recycling.
Determining which strategy is the right one will depend on the existing positioning of individual chemicals players. Those who want to convert their plants to pyrolysis oil do not necessarily have to build up the capacities for chemical recycling themselves, but then they need strategic partnerships.
Exhibit 2: Overview of EU regulations on plastics recycling
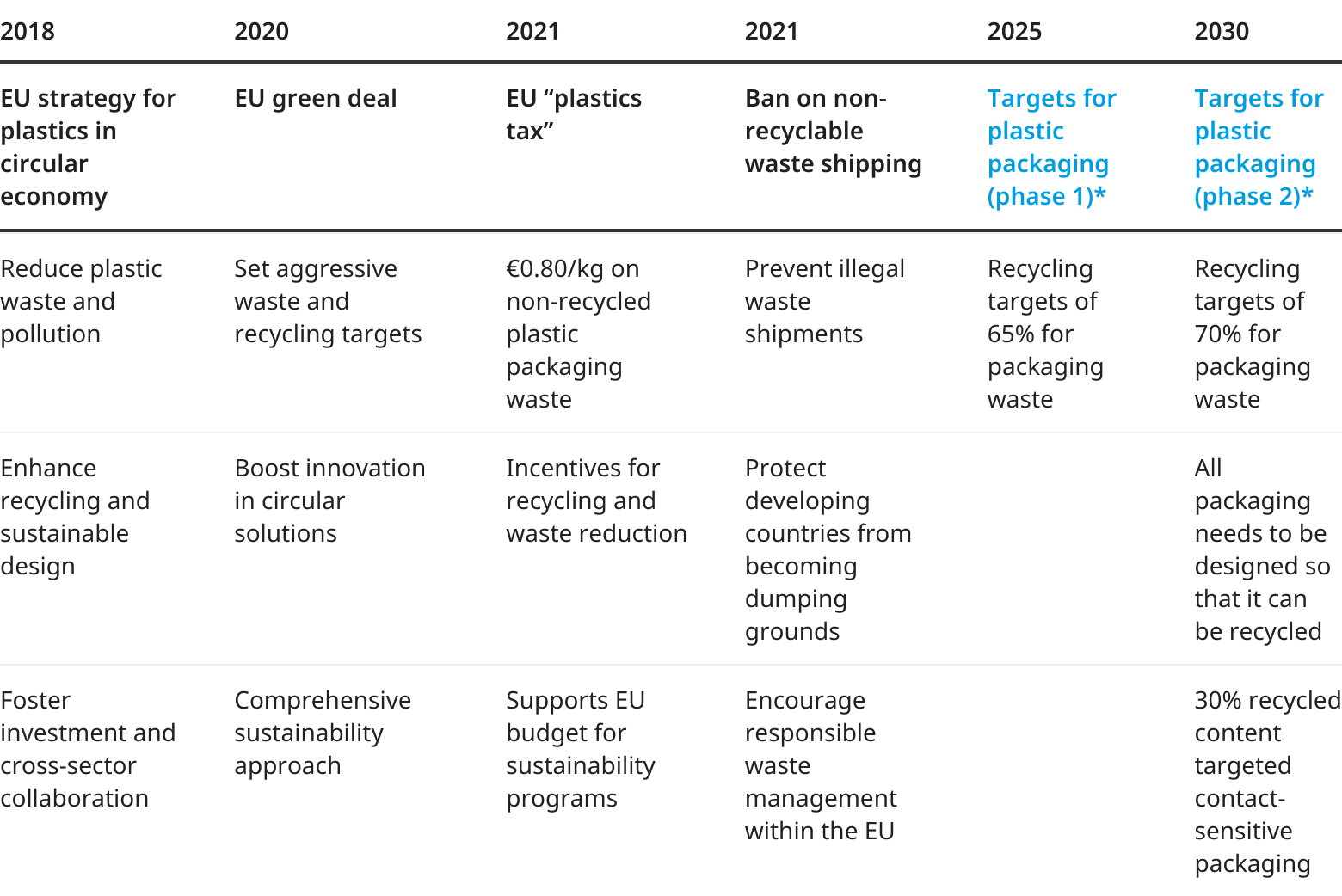
* Targets are not yet effective
Source: Oliver Wyman analysis
The role of governments
In addition to economic factors, rules around plastic recycling and pollution are crucial to success when it comes to building an industrial infrastructure for chemical recycling. Standards for recycled plastics are particularly important. Anyone investing in a plant today must be sure they can still operate it 20 years from now. Governments also must provide incentives to make the investment more attractive in the short run.
For instance, governments could stimulate innovation by offering financial incentives or tax credits toward the development of advanced recycling processes. In parallel, a tax on new, fossil-fuel-generated plastic could increase the economic viability of recycled plastics. Quotas also help. For example, the European Union is mandating a 25% recycling rate for new plastic bottles beginning in 2025 and increasing this to 30% by 2030.
Regardless of the hurdles, the global economy must push for the elimination of single-use plastics and increase the availability of recyclates. That requires closing the looming supply gap and developing chemical recycling — an obvious place for the chemicals industry to become part of the solution and develop a new revenue stream.